Ossid NextGen 500E Tray Overwrapper + Miller Poultry
Chickens are social animals, valuing relationships and connections, and the poultry industry fittingly holds the same values. Longstanding partnerships between the purveyors, retailers and equipment manufacturers in poultry production are the foundation of quality and success within the industry. Orland, Indiana-based chicken processor, Miller Poultry, has found this particularly true in its partnership with Ossid, a leading tray overwrap supplier.
Miller Poultry began its nearly 50-year history back in 1974, when Galen Miller and his father transitioned from raising turkeys to chickens. Since then, Galen Miller and the rest of the Miller family have overseen the company’s impressive growth over generations of poultry production with today’s operations shipping out 3.2 million finished pounds weekly. Its chickens are locally grown and fed a corn and soy-based diet with no antibiotics, no artificial ingredients or coloring, and no hormones
Chief Operations Officer Kevin Diehl said that Miller Poultry’s success and maintaining its family values have been connected since the beginning.
“We want to treat people right, because without our employees and customers nothing else matters,” Diehl says. “Even though we’ve grown to a good size business, the family ownership is still involved on a daily basis. We’ve got a lot of long-time employees; I’ve been with the company 24 years myself. People come here because they enjoy the culture the Miller family and leadership have created.”
Enduring employee relationships is not the only way Miller Poultry has made and maintained industry connections. After meeting Ossid Regional Sales Manager Brian Guillaume at the International Production & Processing Expo (IPPE) show in the early 2000’s and seeing how other facilities use Ossid products, the team felt confident Ossid was the right choice to handle their tray overwrapping needs. Since that initial purchase of three machines nearly 20 years ago, Guillaume has cultivated a close working relationship with Miller Poultry. Today, the company uses a mix of 12 Ossid 500E and NextGen 500E Leak Resistant End-Seal Overwrappers to securely package chicken for sale throughout the Upper Midwest.
Overwrapping Solutions
The packaging solutions provided by Ossid address the needs of a high-demand poultry processor while also embracing the strengths of long-time employees. The 11 500E overwrappers at Miller Poultry each run about 45-50 trays per minute. Fresh chicken is hand placed in a No. 3 tray, 8 tray, 11 tray or 15 tray sizes before going through a 500E that has been engineered to efficiently handle different tray dimensions.
Diehl explains that a primary concern with wrapping chicken is package integrity. Abnormal product shape and unforgiving plastic trays can lead to leaks that turn away customers and potentially ruin product.
“The old machines we used before were PVC film that was just wrapped around the tray, then folded it under the tray before sending it through a heat belt,” Diehl says. “They weren’t fully welded, so you ended up with leakers.”
That’s not an issue with the 500E, which is designed to produce tightly wrapped, end-sealed, case-ready packages for chicken, fish and other protein products.
“It’s a heat shrink film that welds the seams together, so you have a really tight thin seal along the bottom and end sides of the tray, which seals it shut and gives it almost leakproof packaging,” Guillaume said. “The purge of moisture is held within the package instead of leaking through the flange of the tuck and fold.”
Ossid’s unique approach to heat shrinking also includes measures to preserve the preprinted image on the film.
“If you don’t control how it shrinks, you get a lot of distortion and illegible or difficult to read print,” Guillaume said. “The 500E heats that film to hold the seals around the sides of the flange of the tray, so it’s a clean look on the top of the package, but it also keeps all the print legible as it runs through the machine.” A hot water bath after the heat tunnel irons out fine wrinkles in the packaging for a polished look on the final product.
While automation has improved efficiency with tray overwrapping, portions of the packaging process are still a hands-on procedure. In addition to traying, wrapped products are put into baskets and rolled into coolers by employees, and the weight price label department applies labels by hand.
Lasting Partnership
Guillaume and Diehl were able to capitalize on the longevity and skill of Miller Poultry employees to train staff on the inner workings of the 500E packaging machine. All Ossid service technicians are PMMI certified, a qualification that ensures service techs provide the best machinery training for their customers. With this level of training and instruction the Ossid service technicians have been able to position the Miller Poultry team to be proficient in performing nearly all maintenance functions internally without having to schedule a service call, reducing downtime and ensuring the machines are running at peak efficiency.
“I know if we need Brian, we can call him at any point, and he’s going to respond quickly. Our maintenance technicians have had the training and know the machines well enough to do most maintenance in house,” Diehl said
Both Miller Poultry and Ossid anticipate business will continue to grow. Diehl and Guillaume talk often about Miller’s future needs and how Ossid can play a role in the companies continued success.
“We’re very happy with Ossid and how the 500E has performed for us through the years,” Diehl said. “Ossid provides us with machines that produce a solid seal on a package that doesn’t leak. That’s how they are helping us be successful with the high-quality packages for retail.”
Ossid NextGen 500E Tray Overwrappers at Miller Poultry
Miller Poultry
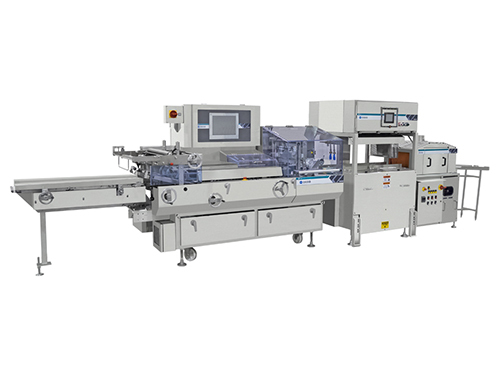